随着智能化、电动化浪潮席卷传统汽车制造业,汽车行业正面临前所未有的激烈角逐。为迎合大众对汽车品质的追求,车企不再满足于聚焦三电系统,转而向智能化、生态化、体验感跃迁,“冰箱、彩电、大沙发”更是成为车企轮番追捧的“标配”。
从整车架构到内饰细节的把控,无不凸显着对汽车品质的极致追求。从传统走向创新,车企及其上下游供应商不断寻求更加智能、高效的三维数字化手段,以提升制造品质和产能。
01案例背景
案例中的客户是沈阳某大型橡胶制品有限公司,公司拥有全国领先的橡胶、塑料技术和先进的生产车间,专为国内外一线汽车品牌和汽车配件公司提供高质量高性能的橡胶、塑料配件。公司是一汽大众的A级供应商,旗下奥迪系列、宝来系列、捷达系列、尼桑系列等轿车橡胶件为国内独家供应商。本次项目需要检测汽车内饰中的走线槽,以确保其尺寸和形状精确度满足严格的汽车制造标准。
02客户需求
走线槽作为关键的内饰组件,不仅影响汽车内部的美观和整洁,还涉及到电线管理和支撑。由于走线槽需要与汽车的内部结构完全匹配,任何微小的尺寸误差都可能导致装配问题,甚至影响整车的功能性和安全性。
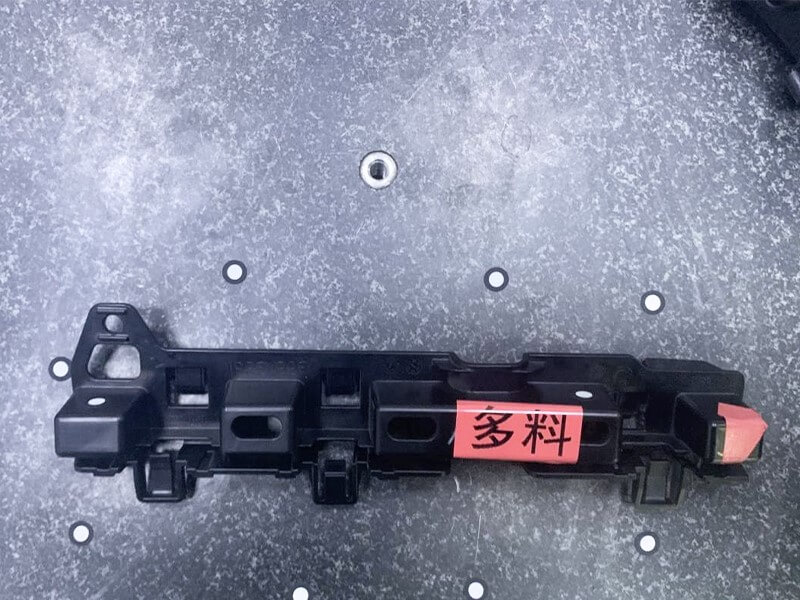
满足车企对供应商产品质量的严格要求,并提高产品的市场竞争力,客户需要一种能够快速、准确地测量走线槽尺寸和形状的方法,同时生成详细的三维数字化检测报告。
客户以往通常采用专用检具进行检测,这种方法存在诸多弊端:
01 测量成本高:在大规模生产中,需要对不同部件进行检测,每次更换检测部件都需要重新定制专用的检具,检具制作成本较高,而且随着产品设计迭代,旧的检具不再适用,更换新的检具会造成较大的成本浪费。
02 精度无法保证:检具自身难以保证精度,且在使用过程中由于磨损消耗容易产生误差。
03 难以完整测量:检具受制于自身结构,对于难以完整覆盖所有细节之处。
04 数据不可追溯:专用检具通常只能检测特定部位的数据,无法生成详细的可视化报告。主机厂在审核供应商的代工资质时,通常要求出具详尽的数据报告,缺少直观的数据报告会使得厂商的质量验证过程变得困难且效率低下。
03项目难点
01 走线槽表面为黑色橡胶材质,普通光学扫描仪容易受到干扰,降低扫描结果的准确性。
02 走线槽内部特征较多,包含多个凹槽、接口及细小的几何特征,这对测量设备的分辨率和精度提出了很高要求,一般测量设备难以确保所有细节都被精准捕捉。
04解决方案及优势
使用设备:SIMSCAN系列掌上三维扫描仪
01 根据工件的特定材质和颜色特性,设置扫描参数。
02 使用三维扫描仪对工件进行扫描,SIMSCAN最高精度可达0.020mm,相机间距远远小于同类型扫描仪,不遗漏走线槽内部凹槽、缝隙等处的微小细节。
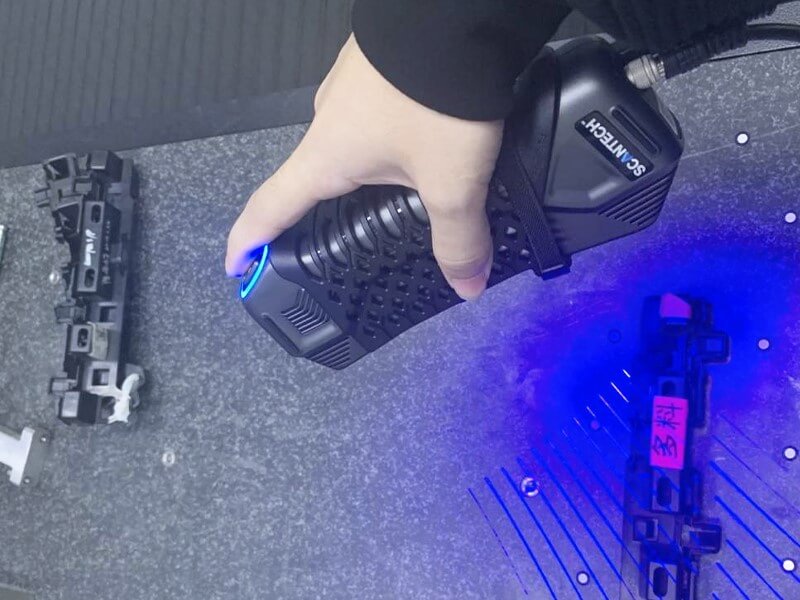
03 快速获取高质量的点云数据并进行网格化处理,结合专业的软件将STL网格数据转化为高精度三维模型,与原始数据模型对比,进行偏差分析。
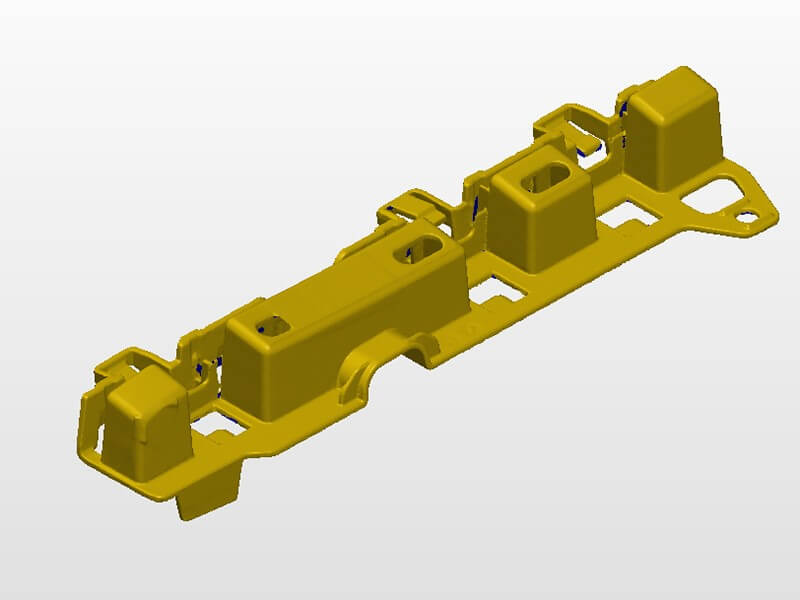

04 最后,导出完整的可视化检测报告,帮助主机厂了解产品的质量状况,评估供应商生产能力。
05客户评价
思看科技三维数字化设备给我们传统汽车制造企业带来了全新的质量检测方案,颠覆了以往低效、繁琐的工艺流程。我们不仅提高了工作效率,还保证了产品质量,直观的检测报告更加有力地支撑我们向主机厂兑现高标准、高质量交付的承诺!
在汽车制造领域,3D数字化技术的应用已经成为高效、精准的代名词,为汽车内外饰生产制造提供了强大的助力。
此外,思看科技三维扫描产品还广泛应用于汽车制造各个环节,如产品开发、汽车模具制造、冲压件检验、汽车车身及零部件检测、定制化改装、维护与维修等,大大简化了企业工作流程,提高了生产质量和效率。
随着三维扫描技术的不断发展和普及,思看科技将不断探索更多应用场景,赋能汽车制造行业将迈入更加数字化、智能化的时代。